We are really glad to expand our offerings in our Ebay Store.
This listing is for High Grade Neoprene Custom Fit Seat Covers for:
ACURA RDX 2007-2010
Genuine CR-Grade Neoprene provides the ultimate fit,
style, and protection for your RDX!
We use genuine CR-Grade Neoprene - not a lower grade. CR-Grade is
used in surfing wetsuits. It has great water resistance and a pleasing,
cushion feel. Genuine CR-Grade Neoprene Custom Seat Covers can be
easily spot cleaned or hand washed and air dried. Several two tone
colors, including Hawaiian Prints. CR-Grade Neoprene is the best choice
for active lifestyles. They are also the easiest seat covers to install.
Note:
This listing includes Front seat covers. If you need Rear seat covers choose Two items on your Checkout. We have the right pattern for all three rows on your MDX. The pictures on this listing are only for reference.
All seat covers are made to your order, fabrication time is 2 weeks aproximately.
Colors to Choose from:
- Solid Black
- Black sides with Gray insert
- Black sides with Charcoal insert
- Black sides with Blue insert
- Black sides with Tan insert
- Black sides with Red insert
- Black sides with Yellow insert
- Black sides with Hawaiian Black insert
- Black sides with Hawaiian Blue insert
- Black sides with Hawaiian Red insert
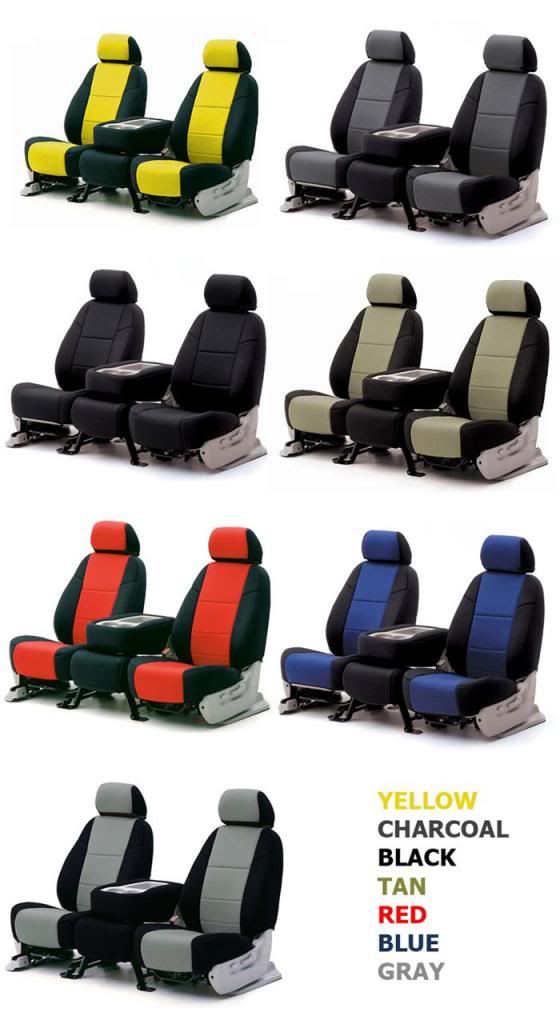
Vehicule Specifics:
This set is specifically designed for a Acura RDX 2007-2010 with built-in side air bags (SRS).
Compliment your active lifestyle with Ultra Custom Genuine Neoprene Seat Covers.
About CR-Grade Neoprene Fabric:
Material
Today's vehicle
seats take a serious beating. Seats are exposed to environmental
hazards like UV rays, user damage like passengers sliding in and out,
kids and pets, spilling food and drink, and many others. The critical
component is the material - specifically, something that stands up to
the abuse, looks great, lasts, is easy to clean and makes installation
simple. We feel the best all-round material is Neoprene.
Neoprene
Unfortunately,
"Neoprene" isn't very specific - its actually a DuPont tradename for
polychloroprene - a synthetic rubber.
Most of us know neoprene as being
the lycra-faced rubber used in surfing and diving wet-suits. It is,
but what most people don't know is that there are several grades. Since
most people aren't polychloroprene experts, some seat cover
manufacturers utilize a low grade neoprene material - the same kind used
in computer mouse pads. If the low grade neoprene worked well for seat
covers, we would use it as well - but it really isn't a good choice for
seat covers. We use the same grade of neoprene as surfing wetsuits
(dry suits, used by scuba divers, use an even higher grade). Mouse pads
aren't subjected to the same environmental conditions and physical
stresses that a seat cover is.
Foam
After sourcing the best price-performance
grade of Neoprene, we have the
Neoprene manufacturer laminate 1/4" of closed-cell foam to the back.
The lamination process is quite interesting. Neoprene is poured in a
liquid state into a giant rectangular shape called a "bun". The bun is
then precision sliced into sheets - we specify 3mm thickness. The
manufacturer then heats the neoprene sheet with a flame, and
simultaneously laminates foam to one side and a lycra-nylon material to
the other. This process is critical. Using lamination by flame ensures
the bond will be strong for years. We had previously had bad
experiences with adhesive lamination, since the adhesive invariably
breaks down when exposed to the elements. While no lamination is
perfect, flame lamination is far superior to any other method.
Unfortunately, it is also much more complex, requires significant
tooling and setup, and results in a higher cost. Adhesive lamination is
as simple as spraying glue - it can be done in low volume with much
less setup and almost no tooling required. Here again, we feel the
benefits are worth the added expense. Finally, the exposed side of the
foam gets a very thin layer of polyester material laminated to it, so
that it is easy to install and remove, and will help to prevent any
color transfer to the original upholstery. If we didn't add this
material (also called "scrim"), the seat cover would adhere to certain
automotive upholstery and would be very difficult to install and remove.
Throughout this process, we would like to bring to your attention that
our entire seat cover is made of the same material. Not just the
"seating surface". The foam layer adds extra cushioning all around,
keeps a uniform look and helps the fit of the seat covers. Even the
material used in the map pocket on the back of the driver and passenger
seat covers is made of the foam-backed neoprene. It looks better, fits
better and provides greater comfort.
Face Fabric
We mentioned
during the lamination process that foam was laminated to
one side of the neoprene sheet and the other side was laminated to a
nylon-lycra fabric. This is the face fabric, and we spent an enormous
amount of development time in getting it right. The face fabric is
subjected to the most abuse. The face fabric requires
UV resistance, but also an understanding of the limits of UV
resistance. Unfortunately, the chemical and process UV inhibitors
available are not capable of completely preventing fade when exposed to
constant, unblocked sunrays. We spent a great deal of time in finding
the most advanced UV inhibitors and using them in fibers and fabric
designed just for us. However, realizing that the fabric will still
fade, we developed special colors which reduce the appearance of fading
over time.
The most difficult colors to deal with in
fading are the lower frequency or longer wavelength colors - such as red
and yellow. The red color we use has been designed to offer a
traditional red color, but also contains other pigments to reduce the
visible effects of fading. While fading is a primary concern for Jeep
seat covers, other matters such as the water and stain repellency caused
us to specify a complex weave of the material. We regularly test the
face fabrics to ensure our suppliers are manufacturing to spec. We
utilize professional testing labs that actually expose our fabric
samples to real world conditions in the Arizona desert in a specially
designed mechanism which is motorized to constantly track the sun and
provide maximum exposure.
Hardware
Sourcing of hardware items such
as zippers, buckles and velcro is critical, since a faulty 1 dollar
buckle
can potentially cause the entire seat cover to fail.
Some models of
seat covers require zippers - even though the zipper will be used only
once over the life of the seat cover, the specification we use for it is
the same as many luggage manufacturers. The plastic in the buckle is
designed to resist cracking in extreme temperatures and yet maintain
some pliability for easy use. All hardware is regularly tested to our
specifications.
We have had the benefit of experience to refine our
specifications - in fact, our specifications for the plastic buckles are
refined at least once a year, based on feedback we receive from our
customers and from warranty claims where we are able to learn from past
failures.
Rest assured that the seat cover you
purchase will benefit from years of experience and real-world use.
Whenever
possible, we select suppliers who have achieved the TS16949 or other
ISO9000 quality certification, and who demonstrate a similar pursuit of
continual improvement - even in a humble zipper.
Construction
The third important
criteria in selecting a seat cover is the construction. With what we
believe are world-class materials and design, our manufacturing team
(100% in the USA) combines the best of computer-aided manufacturing and
traditional human craftsmanship. The computerized patterns are cut on a
large computer-controlled cutting machine, which cuts to ultra-tight
tolerances and repeats the entire process 24 hours a day. After every
stage in the manufacturing process, we perform a quality check, and
every operator has the authority to quarantine the product if they feel
the piece is less than acceptable.
The next step is an inspection
and staging for production, where the cut pieces are attached to a jig
used throughout the rest of the production process.
Every successive
process involves sewing - the jib travels through the various sewing
steps until a finished set of seat covers ends at the final inspection,
packaging, and shipping process. All seat covers include a production
booklet and we offer some online video installation instructions as
well.
Contact us if you have any question about this product.
Thanks for stopping buy!!